Hot Off the 3D Presses, Navy Develops Additive Manufacturing
The U.S. Navy is adopting a new way of delivering parts worldwide: 3D printing.
When a critical component needs immediate replacement, it could take weeks to get through the traditional administrative process and logistics, additive manufacturing can cut those lead times to days—or even hours.
There are also economic savings associated with specific replacements, especially noncritical components.
“We are able to produce parts and prototypes for the Navy, and then, we’ve also standardized our cost structure,” said Aaron Ross, responsible for production, quality and manufacturing products, policies, processes, tools and resources at the Naval Information Warfare Center (NIWC) Atlantic. Ross’ responsibilities are centered on an operation created five years ago that adopts new manufacturing technologies.
“The biggest thing that we’re utilizing 3D printing for is kind of twofold: it’s innovation, but it’s also fighting some of the issues with obsolescence in the Navy,” Ross told SIGNAL Media in an interview.
Ross explained that in an aging fleet, some parts are increasingly scarce. Having the ability to procure replacements in-house saves time and money.
Still, his department keep old technologies alive, but also innovates.
Ross defined these manufacturing techniques as “an opportunity to do things, design things, fabricate things, in a new way” while helping develop cheaper and faster prototypes.
Additive manufacturing, a term that includes 3D printing and other forms of new production capabilities, is a market expected to reach $70 billion globally by 2030, according to a report by Research and Markets.
Seeing its growth and potential, the Department of Defense released an Additive Manufacturing Strategy in January 2021. In the strategy document these procedures are defined as “a form of digital manufacturing relying on 3D models and simulations to produce custom solutions.” The document establishes the importance of adopting this approach to modernize national defense systems, increase materiel readiness and enhance warfighter innovation and capabilities.
Another Navy concern is being able to repair vessels while deployed and, if possible, continue the mission—a growing challenge since modern U.S. adversaries are also major sea powers.
“Expeditionary maintenance refers to the Navy’s ability to perform maintenance operations and battle damage assessment and repair while a ship is forward-deployed,” said the U.S. Navy in a recent release about logistics and maintenance innovation. This document detailed how, in August, the Naval Sea Systems Command tested 65 technologies to keep vessels operational, looking for potentially novel approaches in this field.
For 12 days, the Navy invited suppliers aboard a test ship in California, and many new products and concepts were assessed, including 3D printing.
As the Navy experiments with additive manufacturing technologies, private players are following. Among these, Australian company SPEE3D operates in both ends of the Navy’s longest logistics chain.
SPEE3D designed a portable installation with the Australian armed forces and seeks interested parties in the United States.
“One of the most significant issues the military faces today is the ability to resolve critical spare part requirements in the field, a challenge that worsens in the face of global supply chain issues,” said Byron Kennedy, CEO of the company, which cooperates with the United States, Australia and other armed forces.
The importance of the waters adjacent to Australia was laid out in the U.S. National Security Strategy: “We will affirm freedom of the seas and build shared regional support for open access to the South China Sea—a throughway for nearly two-thirds of global maritime trade and a quarter of all global trade.”
Putting that into action is not only about showing off the brightest and latest in defense assets but also hosting allied vessels efficiently.
“The greatest potential for cooperation lies in advancing our interactions through logistics, maintenance support, training, exercises, integrated deployments, personnel exchanges and information sharing,” wrote a spokesperson for the Australian Ministry of Defense.
In these fields, one stands out as the vessels need a constant flow of parts.
“The [Royal Australian Navy] is working with the U.S. Navy and U.S. Coast Guard to explore opportunities for greater cooperation and assistance on maintenance, repair and logistic support activities. Early discussions are focusing on increased access to [Royal Australian Navy] Fleet Support Unit workshop and maintenance personnel along with mutual recognition of technical competencies,” the Australian Ministry of Defense told SIGNAL Media in an email interview.
Regardless of how an additive manufacturing program is run, whether within the service or employing resources from the private sector, the critical skill is producing a part that will work.
“Our qualification and certification of a part is equal or better to what the traditional part is,” Ross said. Despite combining innovative polymers and metals to high standards, these tools have found limits before being employed. “We’re not talking life-critical, safety things, on board ships or submarines,” Ross added. Still, components like switches or noncritical discontinued parts keep assets maintained with increased efficiency.
“When we have an internal customer that comes to us and they say, ‘Hey, I need this,’ we can take that from concept to realization and a prototype, and what we typically do that in a matter of hours or days,” Ross said.
Sometimes, these time efficiencies also mean major savings. NIWC Atlantic was approached to produce a switch that was discontinued. The supplier offered to manufacture these for $4,000 each, and the challenge was presented to Ross, Smith and their team. They delivered these parts in just over a day for less than $100 each, according to Smith’s account.
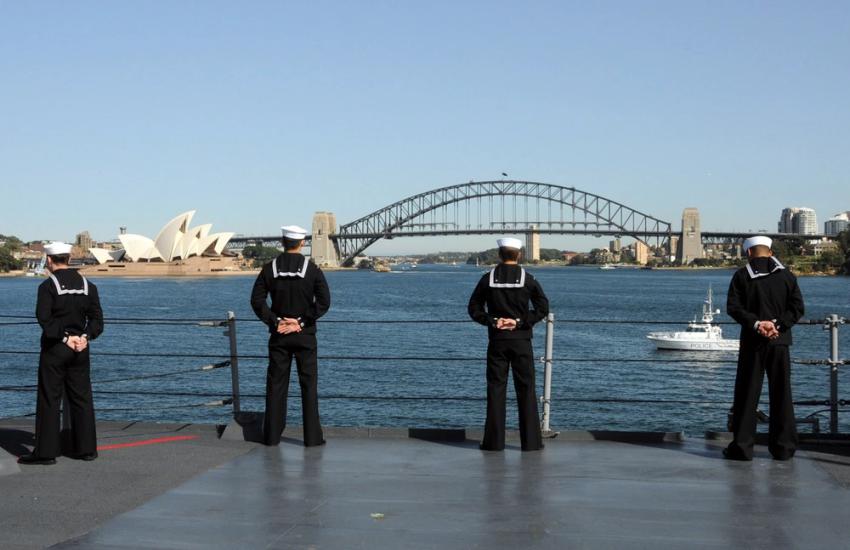
Additive manufacturing does not solve all problems, but when an opportunity presents itself it all starts with an economic analysis.
“We’re trying to build a business case around what makes sense to be printed, but also taking a look at quantities and printing at scale: does it make sense for us to print 1,000 of something? Well, probably not, but does it make sense for us to print two or three?” said Hunter Smith, manufacturing engineering manager at the Naval Information Warfare Systems Command in Charleston, South Carolina.
Thousands of parts aboard a ship can posit solid safety and business cases for 3D printing. But the tallest hurdle does not seem to be in those two criteria.
“We’re dealing with a group that views rapid acquisition and rapid implementation of something as taking five to 10 years, so we spend a good deal of time, not only marketing the capability but also working on changing the mindset of individuals within our command, within the Department of the Navy and how they view 3D,” Smith said.
This technology changes the way many think about lead times, as the Naval Information Warfare Systems Command operates at speeds that were unseen in the institution.
“One of the things about this capability is that it is a government-owned, government-operated group,” Ross explained.
The first-time experience for those used to old techniques and procedures could be a leap.
“We are so quick that it actually takes our [internal] customers—they’re kind of surprised that we can actually do things as quickly as we can,” Ross said.
One critical aspect is not creating the same part every time they are approached. Once a component is fully designed and its standards approved, this and the other additive manufacturing facilities under the Department of Defense are putting together a database of parts.
While this is clearly directed in the Additive Manufacturing Strategy, Ross admitted that this is still in its early stages.
Like every tool in the box, it must match the right job. No device solves all problems. But when all concepts are aligned, the payoff may be above expectations.
“For me, it’s more so being able to look at something and go, ‘That doesn’t make any sense. We shouldn’t be doing that when I can do it faster, better, stronger,’” Smith said.
Comments