From Trash to Treasure: Critical Minerals Recycling
Recycling strategic raw materials is next to impossible, and the United States could not use this method to secure its critical mineral supplies. But alternatives languish as debate rages on in the search for fresh mining opportunities.
The case of rare earth elements (REE) is especially concerning, as most of these 17 elements are crucial in producing modern technologies, especially for defense, and China dominates most of these supply chains.
“You have to reseparate all components, and each one has to be treated somewhat differently, to extract them and purify them, and so it’s not only technologically challenging because of the techniques you would use, but it’s also very expensive,” said Michael McKibben, research professor at the University of California, Riverside.
REEs are crucial to produce semiconductors and other components used in the defense technology sector.
By 2040, experts estimate demand will multiply by up to 7 times compared to current REE consumption.
The United States issued a critical minerals strategy in 2021 that seeks to “diversify supply chains, develop substitutes, improve reuse and recycling,” according to the document drafted by the Department of Energy in collaboration with several agencies and international partners.
The country includes all 17 REEs in the critical minerals list.
This strategy stated that mineral recycling is a strategic goal, but challenges remain.
The main factors hampering recycling, according to Idaho National Laboratory’s Yoshiko Fujita and Daniel Hinosar are:
- Inefficient collection
- The high cost of retrieving the components containing the elements
- Lack of cost-effective methods for recovery
- Very low REE content
Beyond purely economic reasons, in some cases, the refining process of rare earths includes thorium and uranium, two radioactive elements, as a byproduct. While these could be potentially employed to fuel reactors, they add another layer of regulation to this operation—especially in compliance-minded countries.
Nevertheless, this business grows.
The global rare earth metals recycling market was estimated at $248 million in 2021 and is projected to reach $422 million by 2026, according to a report by Research and Markets.
Still, global recycling will be a minor portion of the total market, as by 2026, the total value of the market will be $9.6 billion, according to Markets and Markets.
Therefore, despite the strides in this activity, 95.6% of all raw materials used in 2026 will still be mined.
“Recycling rates in the industry are low, which presents a huge opportunity to invest in recycling capability,” said Harrison Bontje, Mining and Metals Centre of Excellence lead at consultancy EY Americas.
Economics is far from supporting a serious exploration of electronic trash; still, geopolitics has a different rationale.
“The advantage of establishing a domestic supply chain is you improve the market stability and reliability, because you make it very predictable and forecastable,” said McKibben.
There are alternatives to bringing supply chains to the United States, according to other experts.
“When we’re talking about chips, sometimes we talk about onshoring and sometimes we talk about nearshoring or friendshoring,” said Zach Collier, assistant professor of management at Radford University.
Australia’s abundance of mineral resources places the AUKUS [Australia, United Kingdom, United States] partnership at the forefront of the possible friendshoring economies.
“In 2022, Australia produced 27 minerals, 15 of which ranked in the top five for global supply,” Madeleine King, Australian minister for resources, said in a release.
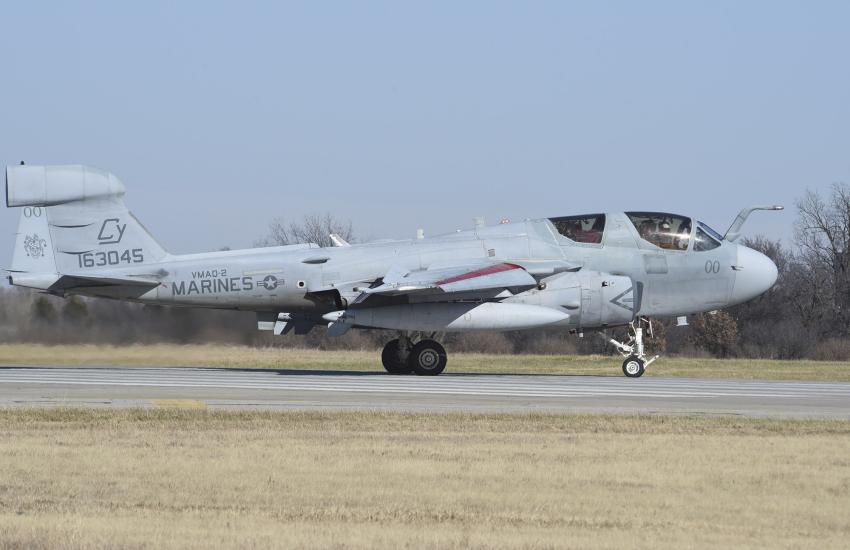
Another strategic mineral as defined by the U.S. Geological Survey (USGS) is lithium. While certain REEs give properties to semiconductors and other electronic components, lithium is crucial in battery production—from electric cars to handheld devices.
Chinese companies supply 80% of the world’s battery cells and account for nearly 60% of the electric vehicle battery market, according to the Atlantic Council, a think tank.
This case underscores the difficulties of working with one element and a production process that is less complex than semiconductors and REEs. And still, the process is plagued by difficulties.
“Getting back the lithium that you started out with, which was about 95.95% pure lithium, to make that battery is the main aspect of the cost,” McKibben explained. Physical separation of the device’s parts is only part of the problem. Stripping chemicals from compounds includes an energy-intensive process, according to this expert.
“The challenge is getting it back to a purity that you can use to remanufacture a new battery,” McKibben told SIGNAL Media in an interview. And given production and use cycles, McKibben warned that batteries, on average, are ready for recycling after a decade.
Bridging the time between production and recycling is not only a problem that should be tackled by industrial processes but also by financial and logistics considerations. Most electric vehicle batteries in use now are not yet ready for reprocessing as they still have many years to complete their life cycle, according to McKibben.
In the case of alternative lithium sources, McKibben underscored that direct extraction could happen from oilfield and geothermal brines. United States, Canada, China and Russia lead in oilfield extraction, but not at scale yet.
REEs and lithium, as well as other critical minerals, are sent to the United States and its allies in components integrated into larger systems. These elements have likely gone through adversaries’ hands at several points in their production processes.
As ancient Chinese strategy posited centuries ago, feeding off an adversary’s supply is far more valuable than producing the goods. Recycling the minerals China and other adversaries have invested heavily in dominating would be a victory, according to Chinese strategist Sun Tzu.
“The wise general sees to it that his troops feed on the enemy, for one bushel of the enemy’s provisions is equivalent to twenty of his; one hundredweight of enemy fodder to twenty hundredweight of his,” Tzu wrote in "The Art of War."
Comments