Steely Determination Brings Metal Foam to Production
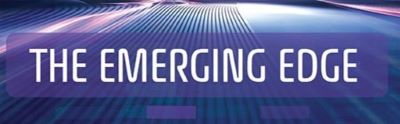
After years of development, metal foam that is lighter and stronger than steel and, according to its inventor, useful for anything made of metal—cars, planes, space shuttles, robots or surgical equipment—is ready for purchase orders.
Afsaneh Rabiei, founder and CEO, Advanced Materials Manufacturing (AMM), and professor, Mechanical and Aerospace Engineering Department, North Carolina State University, has spent 20 years developing composite metal foam technology at the university.
In March of 2021, she leased a 3,500-square-foot manufacturing space in North Raleigh, North Carolina, before raising $3.5 million and recently expanding to 7,000 square feet. “We went through coming from lab scale to a production scale, and now we are working on commercializing the technology.”
Now, she is actively looking for customers and purchase orders in hopes of expanding. “My goal for this year is to bring in orders, as many as we can, and expand our production line. Even though 7,000 square feet compared to my lab space at the university is much larger, this is merely the tip of the iceberg,” she said. “I have requested a sabbatical for this year to put my focus on the company 100% or 200%. and get those orders.”
She already is in discussions with some potential customers, including aircraft and military vehicle manufacturers, she reported.
She added that AMM is prepared to fulfill any orders that might come. “We have scaled up production, and everything is in place to fill orders. I ordered raw materials, literally tons of raw materials, to get ready to fill orders. That’s my goal.”
The light-as-aluminum and strong-as-steel, sandwich armor combines strength, thermal shielding and both ballistic and radiation protection.
Metallic foams are man-made, porous metal materials that contain bubbles. The bubbles can be created in a variety of ways, such as by injecting air or gas or by adding foaming agents. The process is similar to adding baking soda to a cake to make it “fluffy,” Rabiei explained nearly 10 years ago when she was first hoping to commercialize the product.
Most metal foams have uneven cell structures, but Rabiei’s technology uses uniform spheres surrounded by a matrix. The spheres offer “cushionability” and “porosity,” she said, whereas the matrix provides the load-bearing strength and bonds the spheres together. “The problem with other foams is that the structure is very uncontrolled, and as a result, they can deform randomly, and the large porosity can buckle under loading. That’s where my kind of metal foam comes into the picture, with controlled spherical structure and added matrix between porosities to increase strength,” she said.
It has proven capable of shredding 50-caliber bullets and is now being tested against much greater forces. “Before, when I was testing smaller parts manufactured at a university facility, we talked about blast or ballistic testing and so forth, but now we are testing CMF against 8 kilograms of TNT, which is many times larger than what we had done before,” she said in a recent SIGNAL Media interview. “We are trying to put it in a perspective of how it can be implemented into the current structures and how we can solve problems for industry.”
Her company’s website lists eight areas for which the metal foam composite might be useful: aerospace, automobiles, civil engineering, defense/military, nuclear, sporting goods, tools and transportation. But the possibilities do not end there, Rabiei said. “You can imagine anything and everything that you’re using metals for—and even sometimes nonmetal structures—you can replace it with this material.”
And the material can be tailored to fit specific needs. The exact composition might be different for housing electric car batteries, for example, or for space shuttles. “Space shuttles require something lightweight while at the same time protected against impacts and against heat and so forth. A lot of these space shuttles, for example, had been made out of a ceramics outer layer and metallic inner layer because ceramics have high-temperature protection capability, but they are also very brittle,” the CEO pointed out. “By using our material as a supporting structure, your space shuttle is way more protected than with the current structure.
Honestly, I hope, and I wish SpaceX and Tesla can see what we have here and understand how it can help them.”
In 2023, AMM was awarded a Small Business Innovation Research (SBIR) grant from the Department of Energy for the research and development of “Nickel-Based Composite Metal Foam for Nuclear Energy Applications,” which could enhance the efficiency, safety and performance of various components within nuclear energy applications, according to the company website.
A Department of Energy online description of the SBIR award explains that generation IV reactors will likely operate at significantly higher temperatures and pressures while using novel coolants, increasing stresses, fatigue and the effects of reactor coolant chemistry interactions. Therefore, continuous development of “higher performance materials must improve all performance criteria while being easily manufacturable and staying economical.”
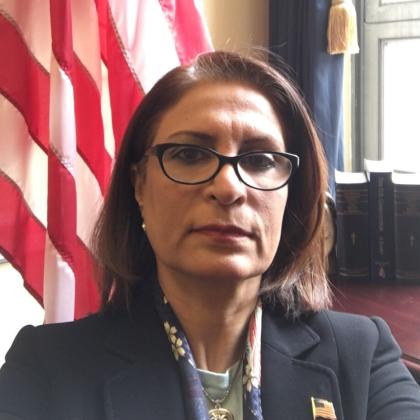
Honestly, I hope, and I wish SpaceX and Tesla can see what we have here and understand how it can help them.
Nickel-based alloys are widely used in nuclear reactors due to their high-temperature strength, corrosion resistance and heat resistance properties but are unable to dampen impacts, vibrations and shocks.
“This material innovation can be used to improve an array of nuclear reactor components, combining the corrosion and temperature resistance properties of Nickel-based alloys with the already impressive list of [composite metal foam] properties,” according to the Department of Energy.
Rabiei reported that the company has successfully conducted a number of nuclear radiation shielding tests, fire protection, vibration dampening, high-power blast and ballistic tests. “All of these scaled-up tests were done starting from September, October of last year, all the way until December. So, these are all fresh, out-of-the-oven experiments that we completed recently.”
Replacing large, heavy containers used for transporting nuclear waste or small nuclear reactors is one possibility the company is exploring. “Sometimes people use huge containers where you carry the nuclear waste or small nuclear reactors. They’re going into these huge tankers with the top and bottom having something called impact limiters, and these are either made of aluminum honeycomb or wood. They have to be really big to absorb the impact energy in case that falls off on the train,” she said.
And while both weight and size matter, sometimes size matters most. “With our materials, oftentimes not only will we lower the weight, but also, we will lower the size, and sometimes the size is more important. We have not only lowered the weight but also lowered the volume.”
The company is exploring the possibility of using the metal foam composites for surgical tools as well. “Those are so heavy, and surgeons are bending over the surgical table for hours and hours, and it would help if we can make something lighter weight and sturdy,” she offered.
To transition the technology from the lab to a commercial product, Rabiei also is transforming from professor to entrepreneur and learning new lessons daily. For example, she has about a half dozen employees whom she tends to treat as if they’re graduate students, attempting to mentor them. But sometimes, she said, she needs to find a balance between being both boss and mentor.
For others trying to overcome that technological Valley of Death, she said failures are to be expected. “It’s definitely a very rough road. It’s maybe one success, 10 failures in every step, but that one success should give us energy to keep going. Every time I fall, I just stand right back up and look for another solution.”
According to the AAM website, it offers:
- 100 times higher impact energy absorption in compression than equal volume parent materials
- 54 times lower thermal conductivity for steel composite metal foam vs equal-weight solid aluminum
- 7.5 times longer fire protection against temperatures up to 2,200 degrees Fahrenheit temperatures vs its solid parent material
- 4 times higher X-Ray and neutron shielding for HZ steel CMF vs equal weigh solid aluminum
- 3+ times lighter weight than its bulk parent material
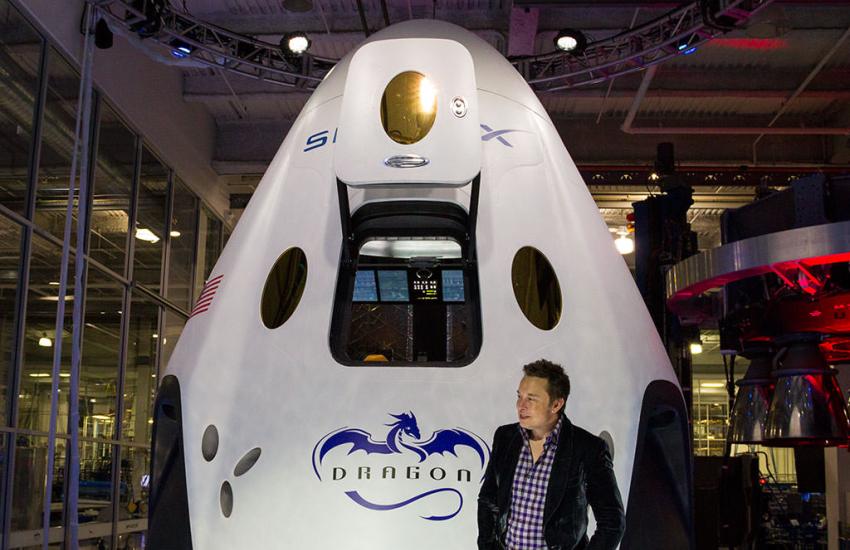
Comments